
More customers are including vitamins into their daily routines as they place a greater emphasis on their health and wellbeing. The market for vitamins is expanding, which has increased the demand for reliable production techniques. Knowing the process used to make these vital supplements guarantees production efficiency and quality. While knowing the steps involved in the production of vitamins is essential, distributors and manufacturers also need to be aware of legal requirements, such as those pertaining to sales tax responsibilities on vitamins and dietary supplements. Regulations differ between states, which might affect your company’s operations and pricing plans.
You may use this website to learn more about this subject and to find out which states impose a sales tax on vitamins.
You may use this website to learn more about this subject and to find out which states impose a sales tax on vitamins.

The procurement of premium raw materials and components is the first stage in the production of vitamins. Strict purity requirements must be met by active substances, which offer nutritional advantages. These are frequently purchased from vendors that, in order to guarantee efficacy and safety, must adhere to regulatory certifications. Fillers, binders, and coating agents are examples of excipients that are essential to the formulation of a consumable and stable product.
To keep manufacturing consistent, ingredient standards are strictly regulated. Changes in the raw material’s quality can have a big impact on the finished product. To guarantee that only the best inputs are used, manufacturers undertake stringent supplier vetting and qualification procedures.
Additionally, with the rise of organic and non-GMO products, consumers increasingly demand transparency in sourcing. Manufacturers are thus expected to provide detailed documentation and traceability for all components used. This satisfies consumer inquiries and aligns with corporate responsibility and sustainability efforts.
Selection criteria now include things like vegan or allergen-free ingredients in addition to the main ingredients. This component is essential for satisfying end customers’ customized demands and catering to specialized markets without sacrificing quality.
The Scope of Quality Assurance in Vitamin Supply

Quality control is the backbone of the vitamin manufacturing process. This phase ensures the final product is safe, accurate, and effective. When raw materials enter the facility, they undergo testing for identity, purity, strength, and composition. Any deviations from established standards are addressed immediately to prevent downstream issues.
During synthesis, in-process controls are essential to monitor the production stages. Techniques like High-Performance Liquid Chromatography (HPLC) and Mass Spectrometry (MS) are often employed to examine the compounds. Periodic testing assures that the product remains within specification throughout manufacture. In this way, consistent quality is maintained batch after batch.
Final products are not exempt from scrutiny. Once vitamins are synthesized, they are subject to a final round of testing. Here, analytical chemists ensure that the label claims match the product contents, verifying factors such as potency and the presence of any contaminants. Only after these rigorous evaluations will products be cleared for packaging.
For manufacturers, maintaining a robust quality control regime is about compliance and building trust with consumers. When consumers choose a vitamin supplement, they expect it to deliver promised health benefits without any harmful side effects, making quality control an indispensable aspect of production.
Labeling and Packaging: Crucial Steps for Preparedness for the Market
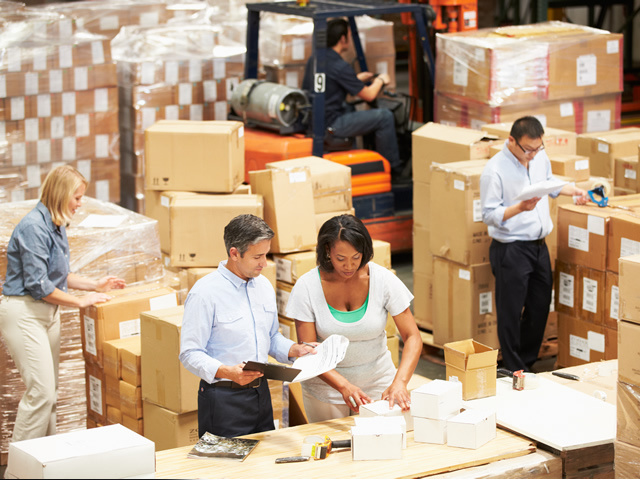
The packaging procedure involves more than simply putting vitamins in bottles; it also involves keeping the product’s integrity intact until the customer receives it. Proper packaging shields the vitamins from light, air, and moisture, all of which can deteriorate their quality. The product’s safety and shelf life are greatly influenced by the materials and packaging techniques used.
It is essential to pay attention to proper labeling in addition to packing. It gives customers vital information such as component lists, dose guidelines, administration instructions, and nutritional value. It also shows compliance with labeling laws that vary on a national and worldwide level. Labeling that complies with regulations is essential for educating consumers and averting legal issues.
The logistics of packaging and labeling are also intertwined with marketing objectives. Brand identity, product differentiation, and target market appeal influence design choices. Hence, packaging and labeling must balance compliance and aesthetics to ensure market readiness and competitiveness.
At this point, customer trends like user-friendly features or environmentally friendly packaging could also be taken into account. Manufacturers have to satisfy legal and safety requirements as well as customer preferences. These kinds of things support a brand’s reputation and foster consumer loyalty.
In general, the production of vitamins involves a complex interplay between strict quality control procedures, careful component selection, and careful packaging considerations. In the highly competitive world of the health supplement market, producers maintain customer confidence and product integrity by placing a high priority on consumer-centricity, openness, and regulatory compliance.